Aluminum production is a highly energy-intensive endeavor, and this energy-intensive nature is palpable within the production facilities, where a powerful magnetic field, quantified in units of gauss, exerts its influence. Hydro Aluminium Metal, a renowned Norwegian company, faced this magnetic challenge head-on by commissioning the 10-axle, self-propelled ModulMAX SP-E. This remarkable machine not only boasts an impressive 250-ton payload capacity but also thrives in a magnetic flux density environment reaching 610 gauss.
Navigating these extreme conditions is no small feat. The sophisticated radio remote control and electronic steering of this cutting-edge self-propelled unit initially struggled with these unique requirements. In such an environment, even the ticking of a mechanical wristwatch comes to a halt, and a 41 mm open-end spanner mysteriously stands upright, seemingly defying gravity—a testament to the magnetic forces at play.

Protection of critical components, such as valves and control cards, became paramount. Joachim Kolb, the project manager, explains the ingenious solutions employed, stating, “Our developers successfully implemented targeted shielding protection measures around the electrical valves and the PC housing electronic control cards, making the vehicle suitable for operation in this exceptional environment.”
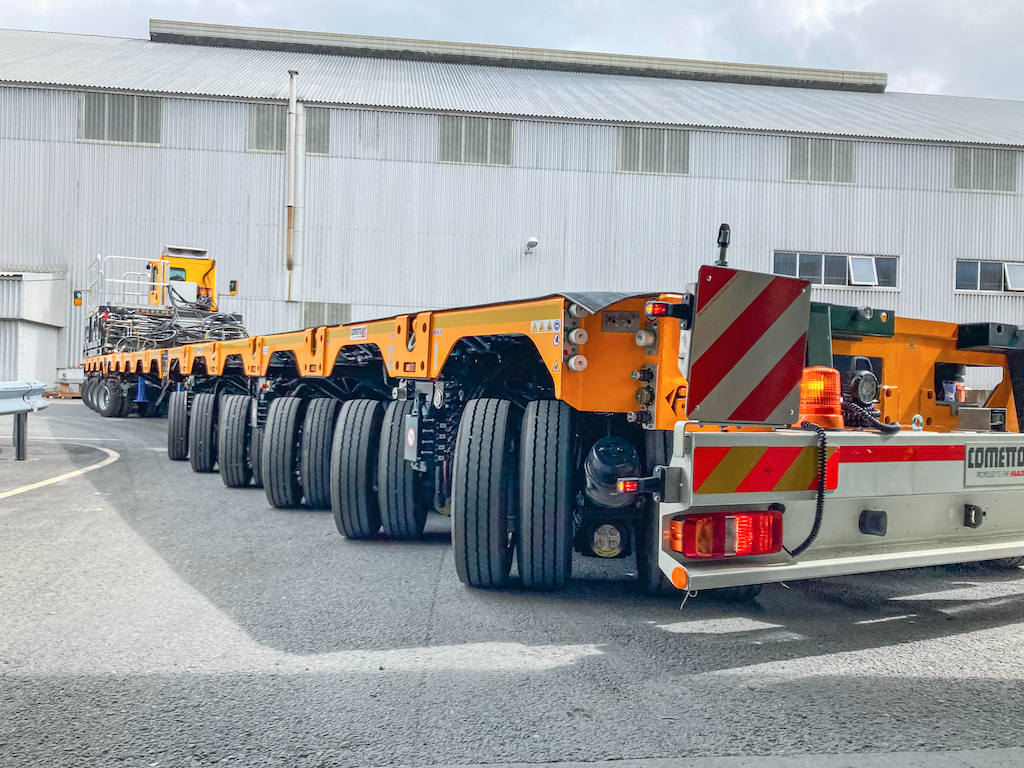
The self-propelled vehicle, measuring a substantial 3,000 millimeters in width, equipped with eight wheels per axle line, relies on Cometto’s expertise to transport the PotShell from the production facility to Hydro’s repair area. There, it undergoes essential maintenance, including the replacement of cathodes and lining. Subsequently, the furnace lower shells are returned to the production hall as part of the process.
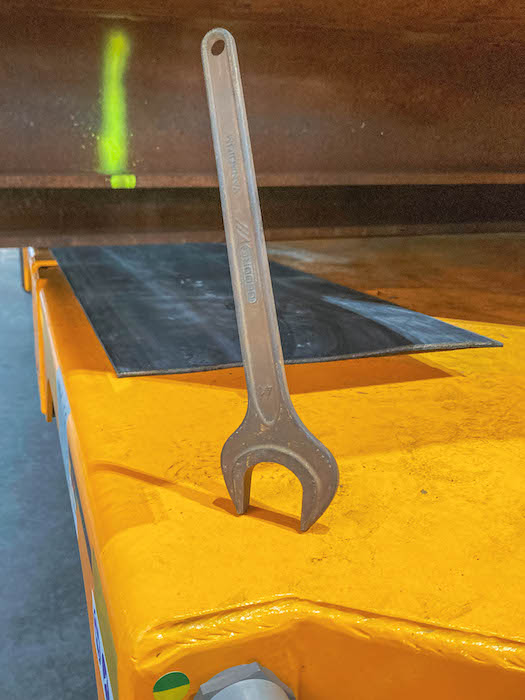
To maximize compactness, the vehicle combination delivered to Hydro comprises a 4-axle module with a spacer and a 6-axle module. The 372 kW Powerpack, housing two Tier 5 diesel engines, and the driver’s cab are ingeniously stacked on top of each other on the chassis. This design not only conserves space but also affords the driver an optimal vantage point for overseeing the transportation process.
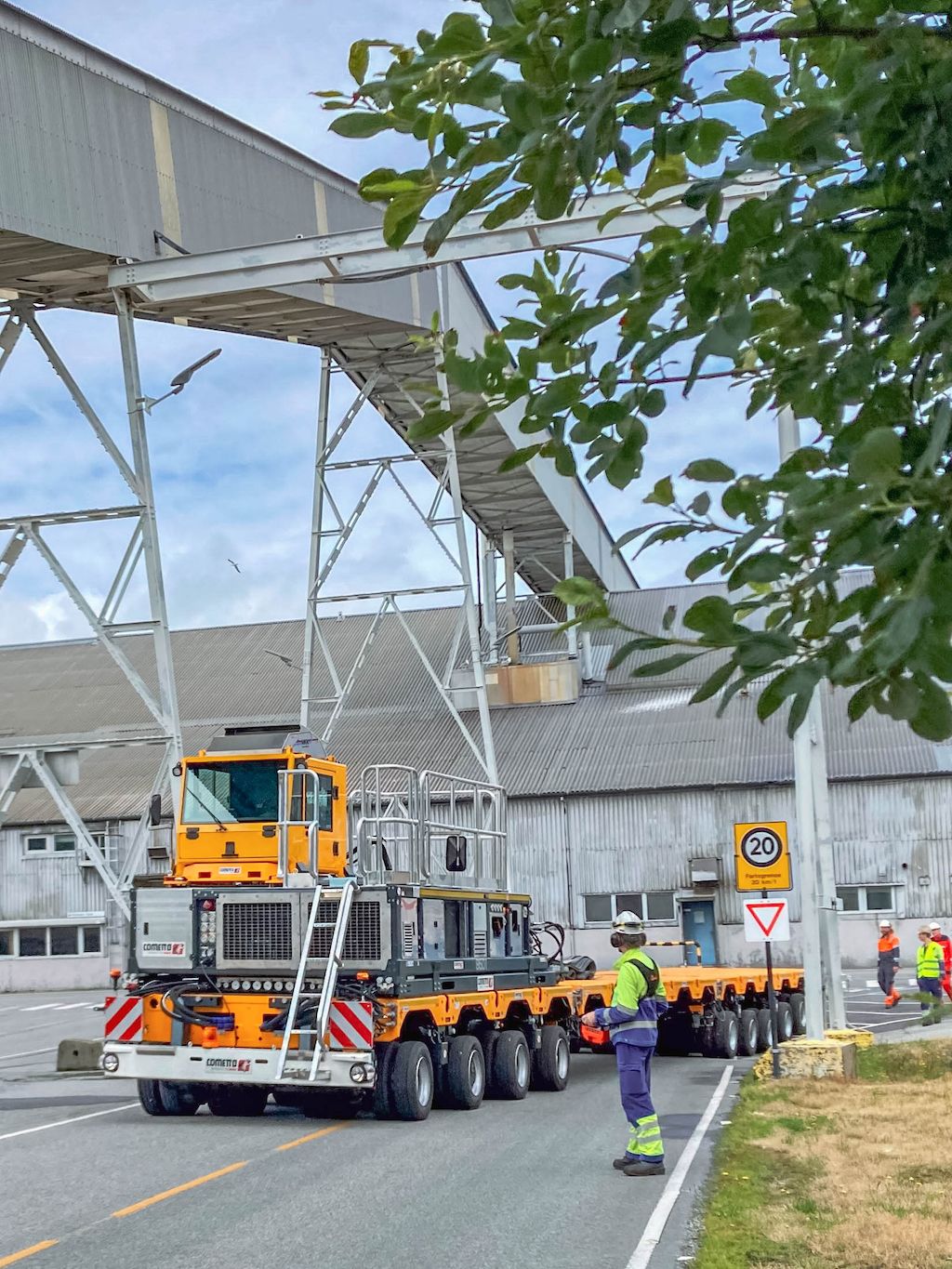
The fruitful collaboration between all parties involved met and exceeded the customer’s expectations, proving the vehicle’s reliability during its operation at Karmøy.
Hydro, a prominent player in the aluminum and renewable energy sectors, has been transforming natural resources into valuable products since 1905. With a global workforce of over 31,000 employees operating in more than 140 locations across 40 countries, Hydro continues to lead the way in sustainable aluminum production and renewable energy solutions.