HS2 (High Speed Two), the UK’s flagship transportation project, connects the West Midlands and London via a 140-mile high-speed rail line. The underground sections of this route are created using massive tunnel boring machines (TBMs), each 170 meters long and weighing 2,000 tonnes. These machines excavate soil and install tunnel walls, consisting of thousands of parts, many of which are extremely heavy and require careful handling during both assembly and dismantling.
Align JV, a joint venture of Bouygues Travaux Publics, VolkerFitzpatrick, and Sir Robert McAlpine, is responsible for the Central 1 section of HS2 Phase 1, including a 16km twin-bore tunnel through the Chiltern Hills. Mammoet supported Align JV in assembling two TBMs at the South Portal site and later dismantling them at the North Portal near Great Missenden.
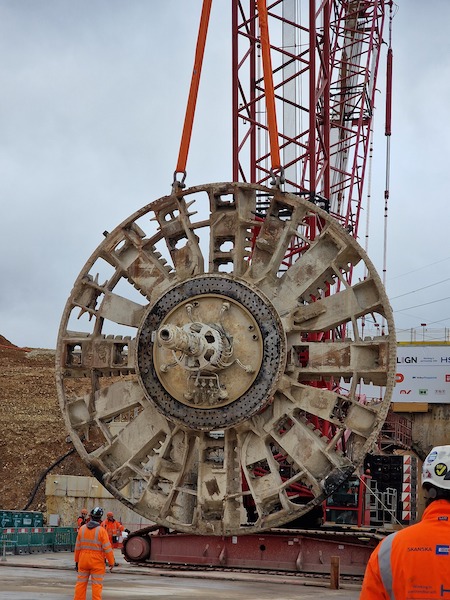
Mammoet’s Senior Commercial Manager, Simon Crawley, assessed the North Portal site’s limitations and space constraints, determining that a 400t crawler crane would be sufficient for dismantling, as opposed to the 600t crane used for assembly. Using Move3D software, Crawley, Project Manager Rhys Burley, and Project Engineer Antreas Michail created a detailed visualization and animation of the dismantling process, convincing Align JV of the feasibility of using a smaller, more cost-effective crane.
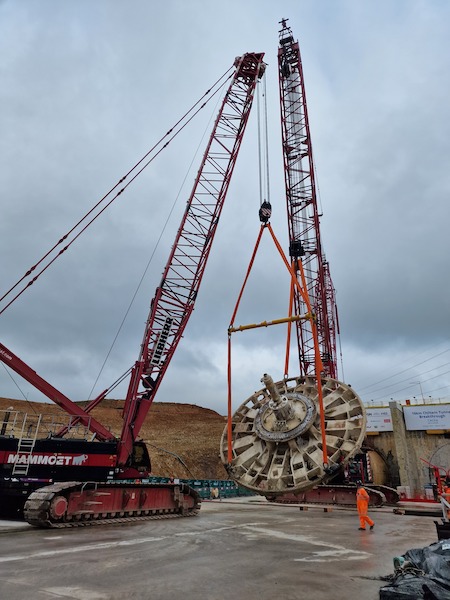
Two TBMs, responsible for the south and northbound tunnels, required dismantling. A 400t capacity CC2400 crawler crane removed the largest components, with an LR1300SX crane assisting in lifting the heaviest cutter head. Components were then transported using Mammoet Self-Propelled Modular Transporters (SPMTs) to laydown areas, where additional cranes offloaded them for further dismantling. The cutter head’s unknown center of gravity and the TBM’s exit angle posed challenges, which were addressed by using air hoists for safer and more efficient component leveling.
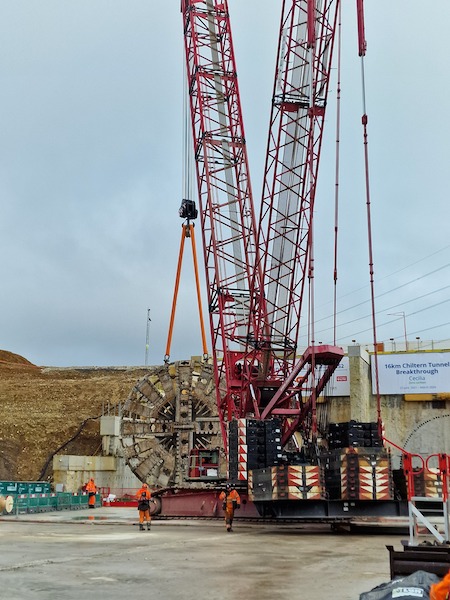
Mammoet’s comprehensive approach, combining skilled personnel, specialized equipment, and innovative thinking, ensured a safe and efficient outcome. By making small adjustments to the project scope and proving their benefits through visualization, Mammoet delivered a successful dismantling operation, showcasing their capability to adapt and meet the complex demands of large-scale infrastructure projects.