The production of aluminium is known for its energy-intensive nature, which becomes particularly evident in the presence of a strong magnetic field, measured in units of gauss, within production facilities. Hydro Aluminium Metal, a Norwegian company, faced this challenge head-on when they commissioned a 10-axle self-propelled ModulMAX SP-E for their operations. This robust vehicle not only boasts a substantial 250-tonne payload capacity but also demonstrates the unique ability to operate effectively in a magnetic flux density environment of 610 gauss.
Navigating such extreme conditions is no simple feat, as conventional radio remote control and electronic steering systems often struggle in this specialized setting. In this environment, even everyday objects, like mechanical wristwatches and spanners, can behave strangely, demonstrating the remarkable influence of magnetic forces.
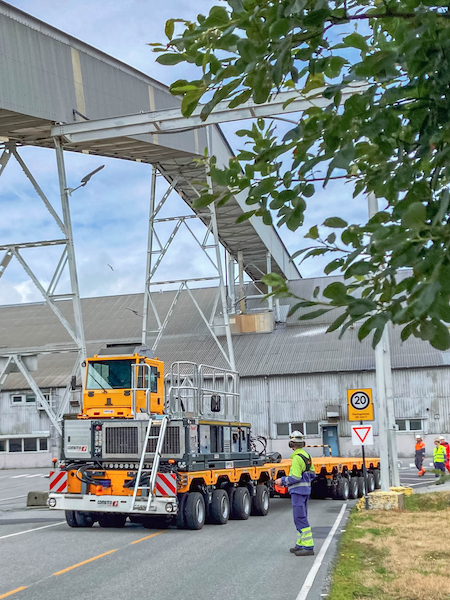
To address these challenges, the project’s manager, Joachim Kolb, shared insights into the development process, highlighting the implementation of targeted shielding protection measures around the electrical valves and the PC housing electronic control cards. These measures effectively rendered the vehicle suitable for operation in this unique environment, allowing it to meet Hydro’s specific requirements.
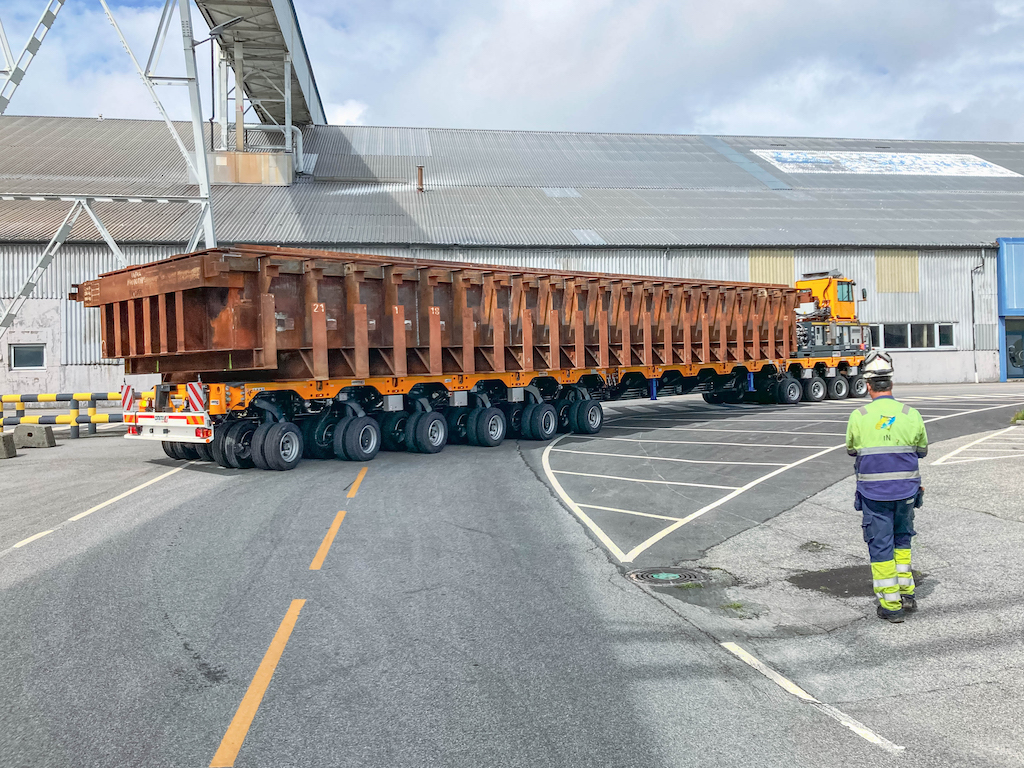
The self-propelled vehicle, measuring 3,000 millimeters in width and featuring eight wheels per axle line, was equipped with Cometto’s expertise to transport the PotShell from the production hall to the repair area at Hydro’s facility. There, the PotShell undergoes maintenance, receiving new cathodes and a fresh lining before being returned to the production hall.
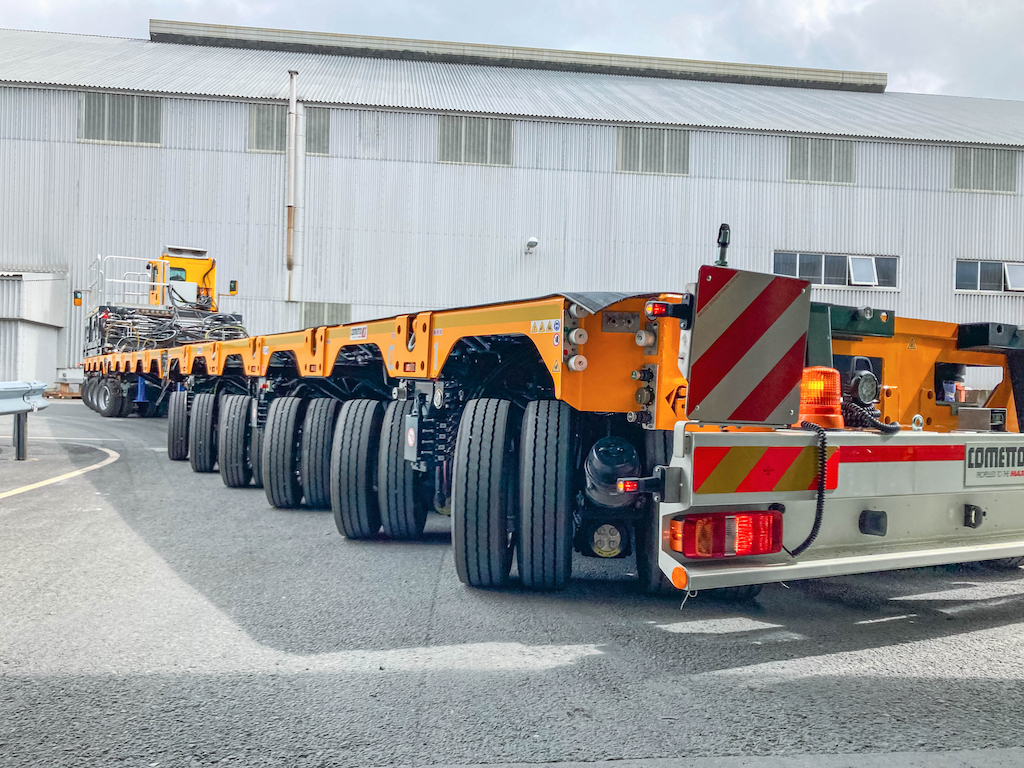
The vehicle combination delivered to Hydro consists of a 4-axle module with a spacer and a 6-axle module. To maintain a compact overall length, the 372 kW Powerpack, housing two Tier 5 diesel engines, and the driver’s cab were stacked on top of each other on the chassis. This design not only optimizes transport efficiency but also provides the driver with the best possible visibility during operations.