USA-based heavy lift and rigging equipment rental and sales company, Engineered Rigging, combined its expertise to help a contractor dismantle and remove the 90-year-old Wittpenn Bridge in New Jersey. The challenging work included lowering two counterweights estimated to weigh nearly 450 tons each and a 209-foot-long vertical lift span weighing nearly 900 tons. Adding to the difficulties, crews maneuvered in close proximity to a nearby railroad trestle and battled winter storms and frigid temperatures.
Before removal of the counterweights and main span began, Engineered Rigging assessed the vertical lift bridge’s structural integrity. For nine decades the bridge weathered countless storms, nor’easters and hurricanes, and carried over 50,000 vehicles a day between Jersey City on the east and Kearny on the west. The company conducted several engineering studies to identify risks and optimize safety precautions. They analyzed the existing structure using computerized modeling to ensure the forces put on the bridge during the controlled lowering would not damage the structure. “Our analysis revealed that the bridge was not strong enough to simply grab and lower,” said Christopher Cox, P.E., co-founder and president of Engineered Rigging. “We needed to add steel beams and clamping fixtures to ensure its structural integrity.”
Due to its high capacity, compact footprint and ability to provide precise control for load lowering up to 100 feet, Engineered Rigging deployed a strand jack system as the most suitable heavy lifting equipment for this project. Whenever possible, the strand jacks would attach to the existing bridge structure including the main tower sheaves and ropes, lift girders, towers and floor trusses. To expedite project design, teams of engineers and project management simultaneously developed two engineering plans—one to lower the counterweights on the east and west ends of the bridge and another to lower the main span. This parallel development facilitated the New Jersey Department of Transportation’s (DOT’s) extensive submittal review.
Custom fabrications connect system to the ageing structure
Once the lift plans were complete, the necessary steel fabrication work began at Engineered Rigging’s fabrication shop in Russellville, Arkansas. The company completed more than 400,000 lbs. of steel fabrication in just five weeks. For the lowering of the counterweights, Engineered Rigging fabricated custom attachments called dog bones to secure four inverted 200-ton strand jacks under the main span lift girders. They also fabricated a transfer fixture designed to allow the decoupling of the main rope spelter sockets from the lift span and allow the lowering of the counterweights to just above the bridge deck for demolition.
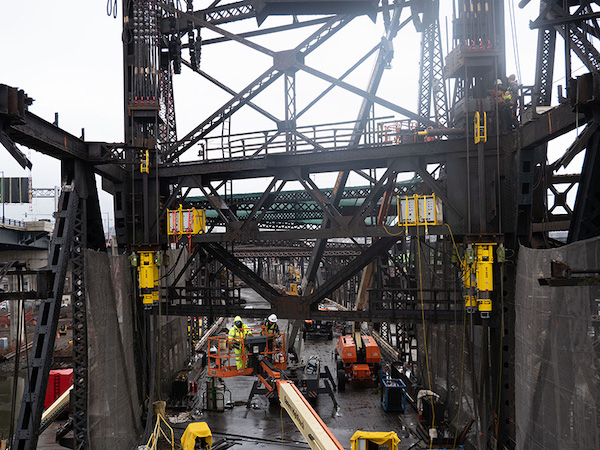
Overcoming the unexpected
Last November, Engineered Rigging arranged delivery of 16 200-ton strand jacks and several truckloads of steel fabrications to the job site. Crews tested the equipment and familiarized themselves with it before mobilization to ensure efficiency and safety but it was during the field implementation phase that the team encountered a few surprises. Despite extensive field reviews of the bridge, the corrosion and deterioration were startling and caused more than one course correction. One major discovery of a previously unknown bridge repair due to apparent collision with river traffic delayed the project until January. Finally, the 450-ton east counterweight was safely and successfully lowered on January 7, 2022. The lowering operation took just under five hours. On January 10, the process was repeated to lower the west counterweight.
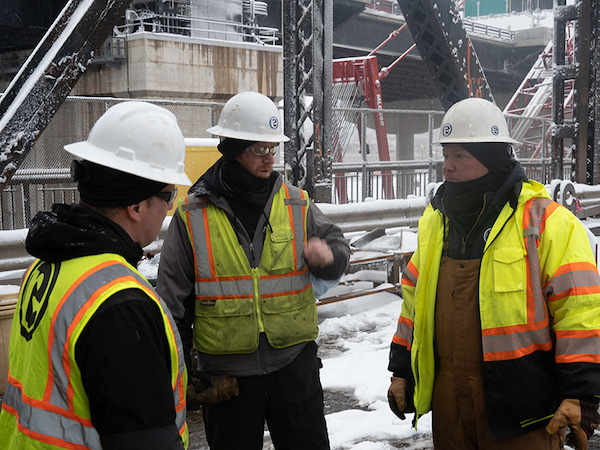
While the contractor was busy demolishing 900 tons of lowered counterweight, Engineered Rigging’s technicians attached structural steel reinforcement, beams, clamping fixtures and connection points to the tower and lift spans for use in the second phase of the deconstruction — lowering the lift span. Crews moved strand jacks and dog bone fixtures to the lift span and attached with rigging to the corresponding beams.
An additional eight strand jacks were mounted in cages to the tower span beams and tensioned over the tower sheaves to the lift span strand jacks. In total, Engineered Rigging used 16 strand jacks on the main span lowering operation of the Wittpenn Bridge. Eight strand jacks engaged the lift span as static rigging and another eight were tied into the tower spans to lower the bridge.
Prior to cutting the bridge, forces of over 900 tons were applied to the lift span to test connections and ensure the system was ready for the massive lowering project. On the morning of January 23, the 209-foot long, 900-ton trimmed lift span was safely lowered to an awaiting barge. “The Wittpenn Bridge project is a great example of the time savings and project efficiencies that Engineered Rigging can deliver to civil contractors,” shared Eddy Kitchen, co-founder and principal of Engineered Rigging. “Our team of in-house engineers, combined with heavy lifting equipment rentals and innovative design-build solutions allows us to deliver synergies that others cannot match.”
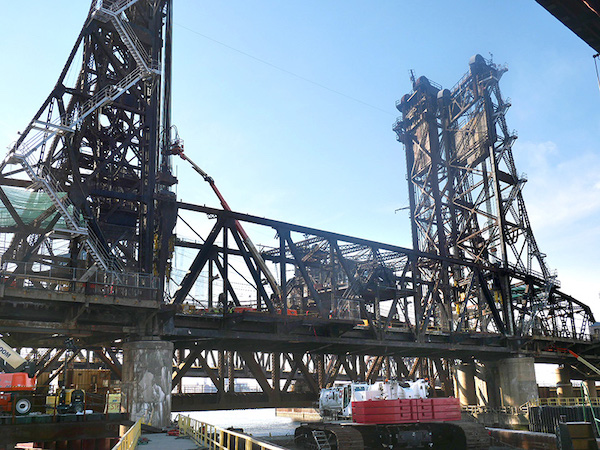