Engineered Rigging has expanded its Equipment Service Center in Russellville, Arkansas, to include dynamic testing and certification for hydraulic cylinders, pumps, and other high-pressure hydraulic equipment. Equipment owners can now send their tools to the center for thorough testing and servicing by skilled technicians trained in Holmatro’s dynamic testing methods.
Dynamic testing simulates a maximum load (105% of capacity) in a controlled setting to uncover internal scratches or damage in hydraulic cylinders that might lead to leaks or failures. During the test, the cylinder is pressurized along its full stroke, providing a more comprehensive check compared to static testing, which only pressurizes at set levels.
The process involves four key steps:
- A detailed inspection of components like pumps, hoses, and manifolds.
- A dynamic test simulating full-capacity load across the cylinder’s stroke.
- Repairs or replacements of worn or faulty parts.
- Cleaning and preparing the equipment for return in optimal condition.
After testing, a Safety & Performance Tested Certificate is issued, offering clients documented assurance of equipment reliability.
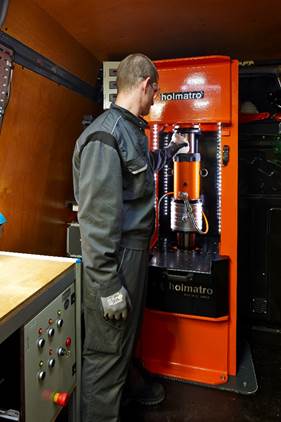
“Dynamic testing is a breakthrough for preventive maintenance,” said Mike Beres, vice president of Engineered Rigging. “It improves safety, boosts performance, and extends equipment lifespan.”
Christopher Cox, president of Engineered Rigging, added: “Safety is a core value for us. Offering clients an affordable way to enhance maintenance programs is a priority.”
The facility also provides load tests for hydraulic gantries and services equipment like skidding and jacking systems. Engineered Rigging is an Authorized Enerpac Service Center and a Holmatro Premium Service Partner. Live dynamic testing demonstrations will take place during Engineered Rigging’s Equipment Showcase, May 6-8, 2025.
Investing in preventive maintenance reduces costs and ensures workplace safety. Studies show running equipment to failure can cost up to 10 times more than regular maintenance, while companies save $4–$6 for every $1 spent on safety.