The decommissioning of the nuclear power plant Unterweser in Germany marked the first of five pressurized water reactor plants that would be shut down. For operator PreussenElektra, it was important to find a pilot solution that could be adapted to the other power plants within the fleet. To lift the reactor pressure vessel, weighing approximately 400 tons, out of the reactor pool as a whole component, Mammoet was tasked by contractor Höfer & Bechtel based on its high standards for quality and safety in engineering.
Mammoet proposed a customized solution using the SBL 1100, a moveable four-point hydraulic lifting gantry with a capacity of 1100 tons. This technical solution was well adapted to the confined space conditions and was therefore suitable for use in PreussenElektra’s fleet. However, there were strict limits on load-bearing capacity due to the tracks of the lifting gantry resting upon the operating floor and partly spanning the reactor pool itself via a cantilever. Mammoet’s engineering team carried out calculations and successfully proved that load distribution ramps could be used to ensure safe execution.
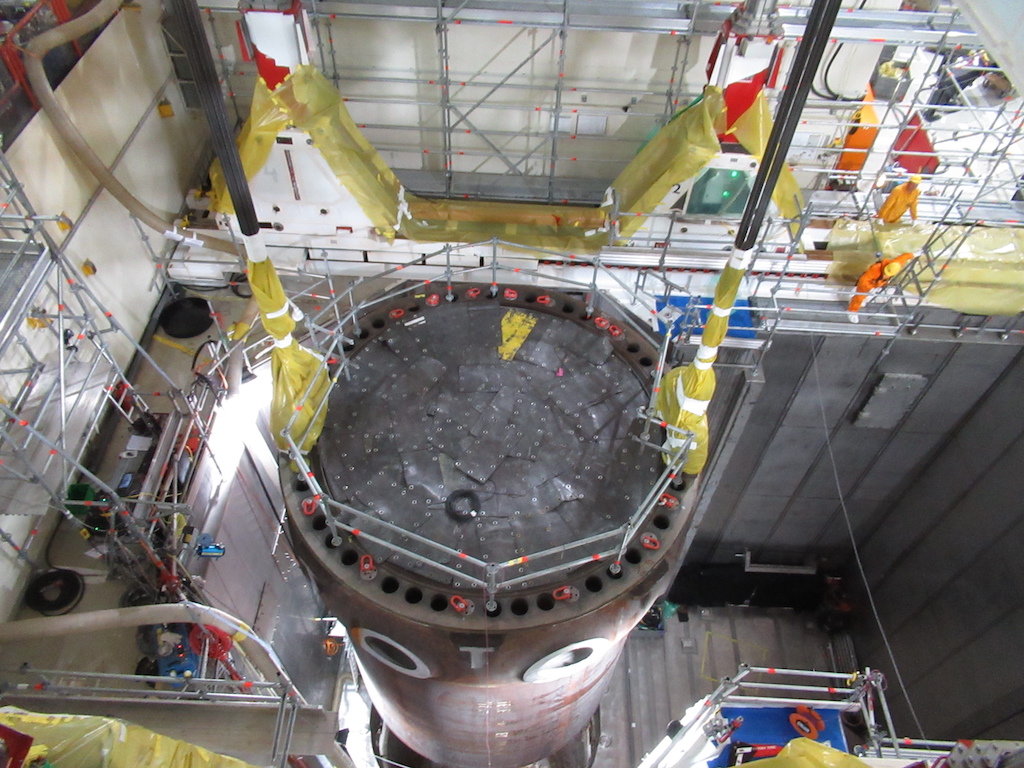
The strict verification and documentation requirements for the material used in the control area posed another challenge. Mammoet and the contractor coordinated with authorized experts and met high-quality requirements by providing necessary material verifications and production manuals. Once the documentation was completed, all equipment was brought into the control area, piece by piece, and foiled so that it could be decontaminated and removed after completion if necessary.
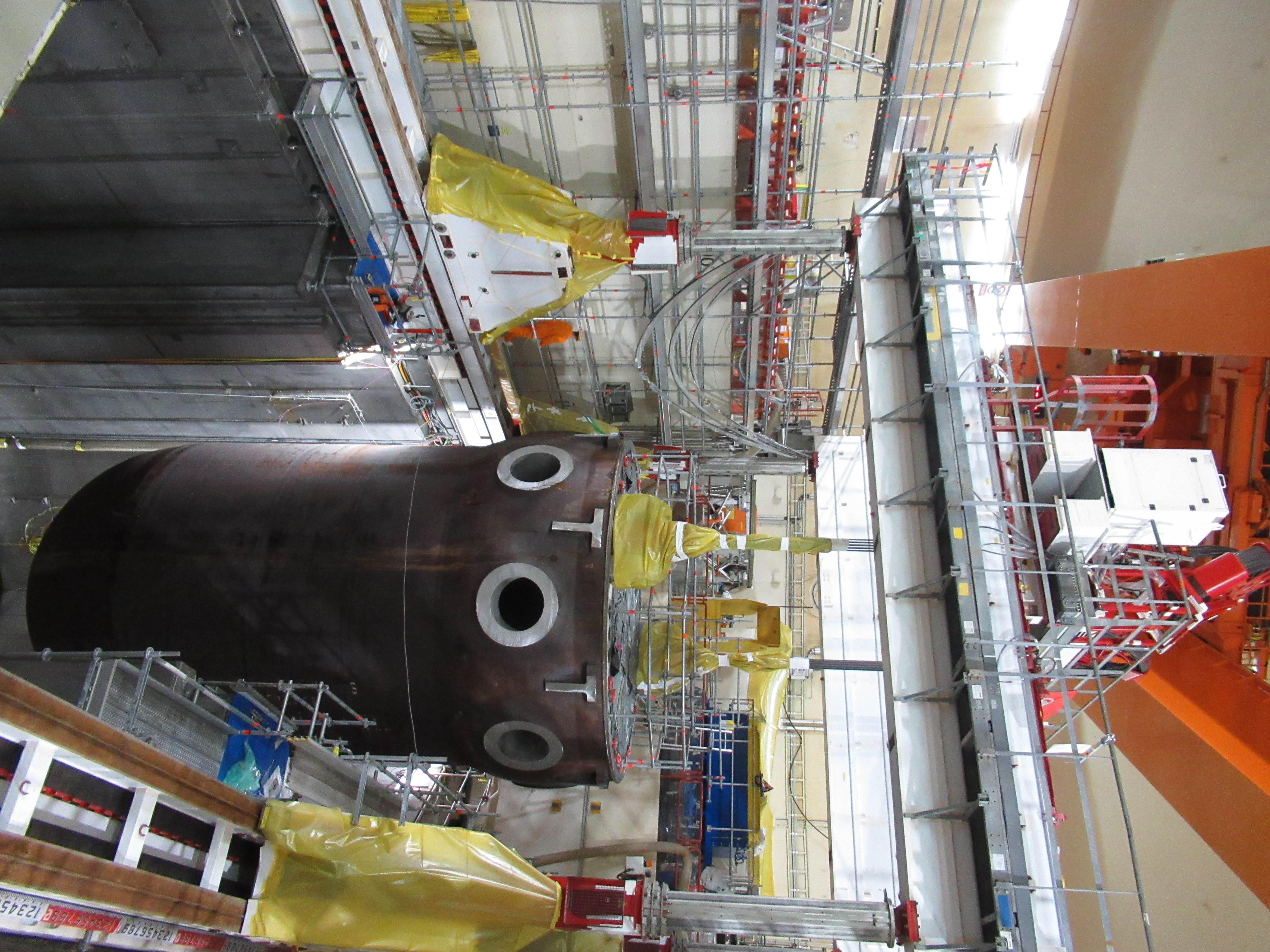
Before the lifting system was installed on the operating floor, steel load distributors had to be installed first. These were followed by tracks, four hydraulic lifting stamps, and two strand jacks to increase the lifting height of the system. The strand jacks were installed on a hydraulic skidding track on the beams of the lifting system, allowing the reactor pressure vessel to be lifted and lowered vertically and also moved laterally.
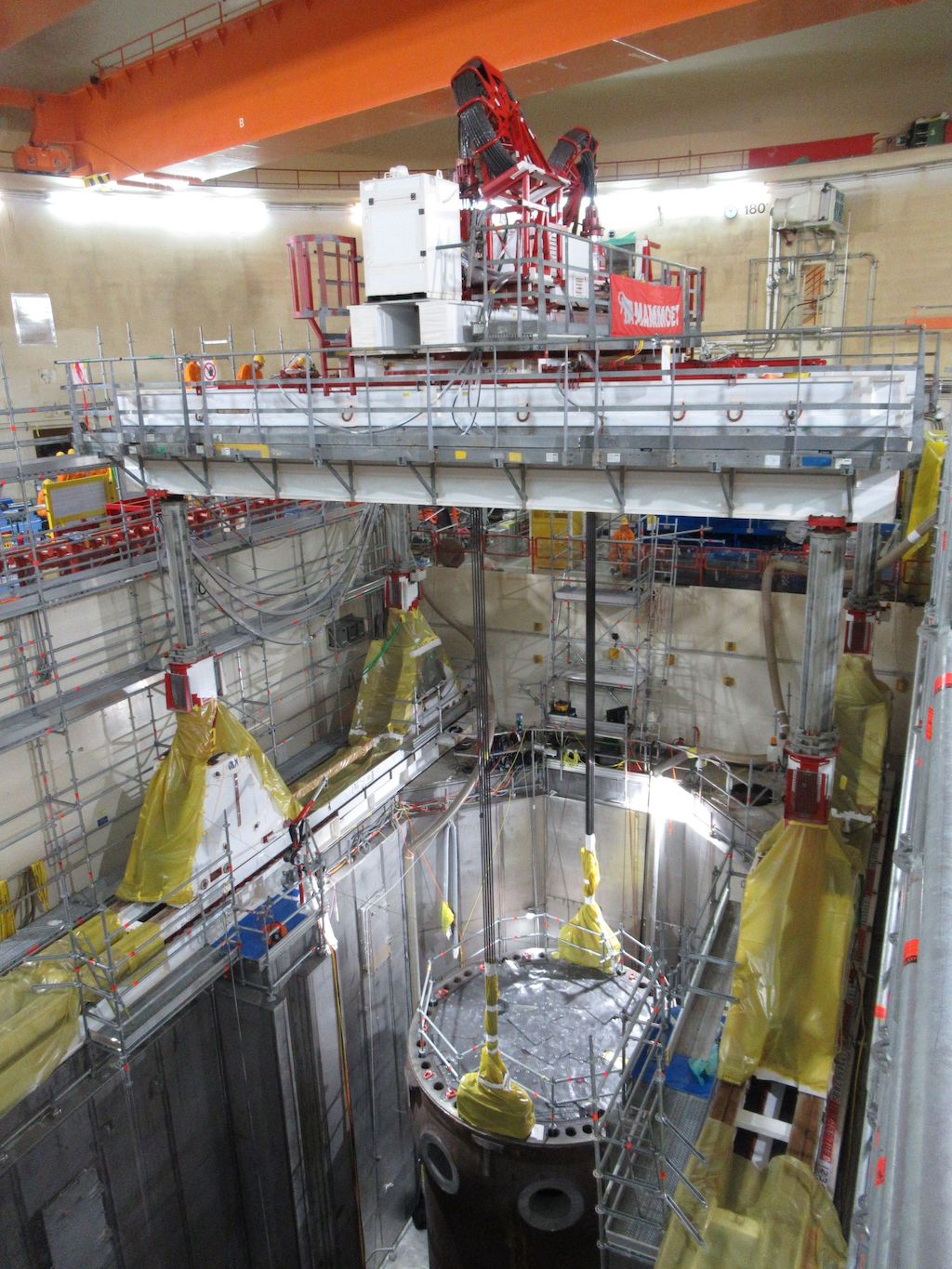
After successful load testing for all components, Mammoet received the final approval for execution. The execution was carried out exactly according to the planning in several steps: first, the reactor pressure vessel was lifted from its installation position in the reactor pool. Next, it was moved horizontally to a parking position. Meanwhile, the contractor placed a dismantling rack with the reactor building crane at the original installation position. The reactor pressure vessel was then moved back to its installation position and lowered onto the dismantling rack so that the contractor could safely cut off the calotte. Finally, the reactor pressure vessel was moved to the final dismantling position and lowered, lifting over a wall in the process.
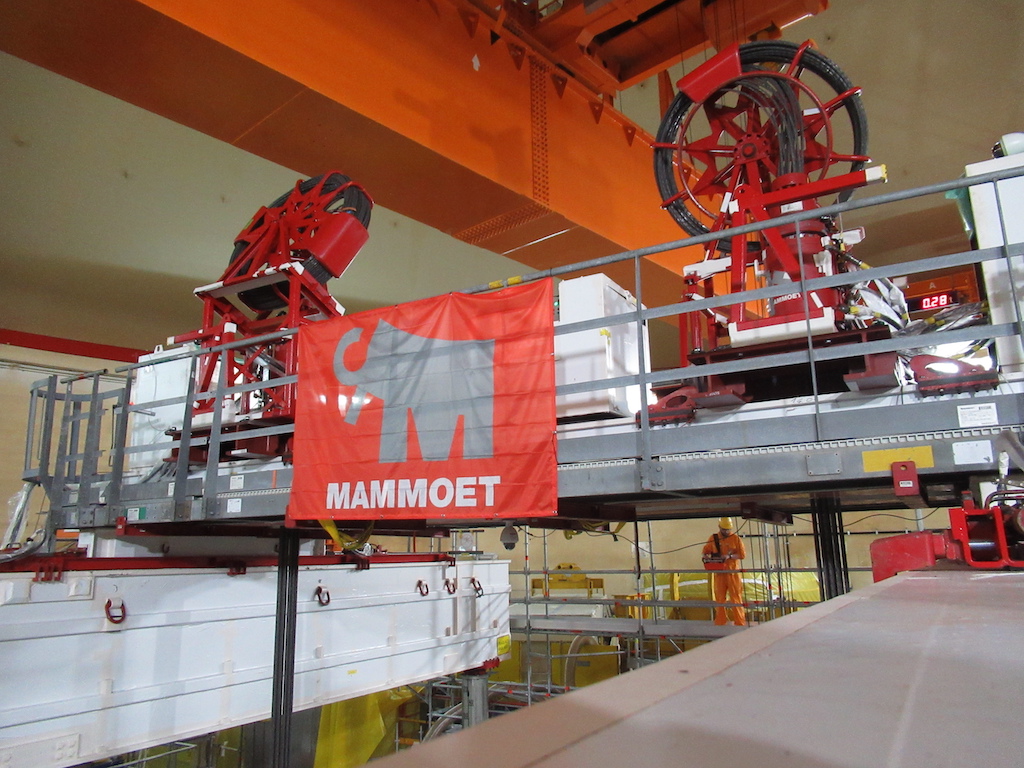
Mammoet ensured a smooth, safe, and on-time execution at the construction site by bringing together the right expertise from throughout the global business. The expertise gained from this pilot project will be utilized for the contractor on another of the operator’s decommissioning projects. Philipp Boettcher, Manager Engineering at Mammoet in Germany, said, “The removal of the reactor pressure vessel was a very demanding project. Through the intensive cooperation, all parties involved have grown together and become a team. We are delighted that we were able to contribute to a safe project with our custom lifting solution and pave the way for another decommissioning project within the power plant fleet.“