Project heavy lift carrier AAL Shipping (AAL) recently completed a challenging transport of a 560-tonne crane body from Kobe, Japan, to New Orleans, USA, as part of its regular Asia – Americas Trade Lane Service. The cargo was delivered onboard the 31,000 dwt heavy lift vessel, AAL Kembla. The operation posed unique challenges due to the immense size and complex configuration of the cargo, which required meticulous engineering and precise adjustments to ensure safe transport.
The consignment consisted of a 560-tonne crane body—measuring 20.14 meters in length, 15.5 meters in width, and 19 meters in height—along with a 60-tonne crane boom and five large grab buckets, each exceeding 100 tonnes. The components were all destined for Curtin Maritime, a USA-based marine solutions company.
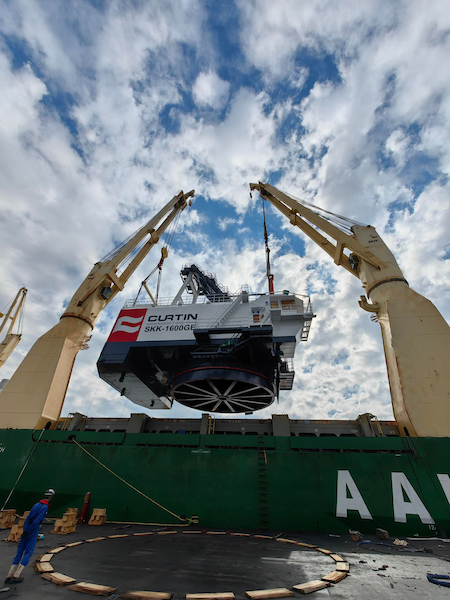
In Kobe, a barge carrying the components was positioned alongside AAL Kembla for loading. The placement of each unit on board was carefully planned to align with the outreach of the vessel’s 350-tonne capacity cranes. To manage the immense load, the cranes were deployed in tandem, providing a maximum payload of 700 tonnes, with two distinct lifting points: one for 302 tonnes and another for 258 tonnes.
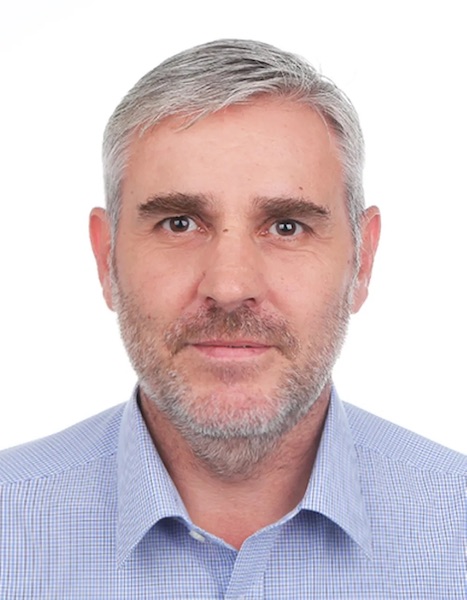
Adverse weather conditions threatened to disrupt the operation, prompting AAL’s Engineering team to swiftly adjust the lifting plan to avoid delays. “Our team’s quick response in modifying the lifting plan was critical to maintaining safety standards while staying on schedule,” said Nicola Pacifico, Head of Transport Engineering at AAL. “This level of flexibility allowed us to meet our commitments and ensure timely delivery as part of our Asia – Americas Trade Route, with the shipment arriving in New Orleans by the end of December 2024.”
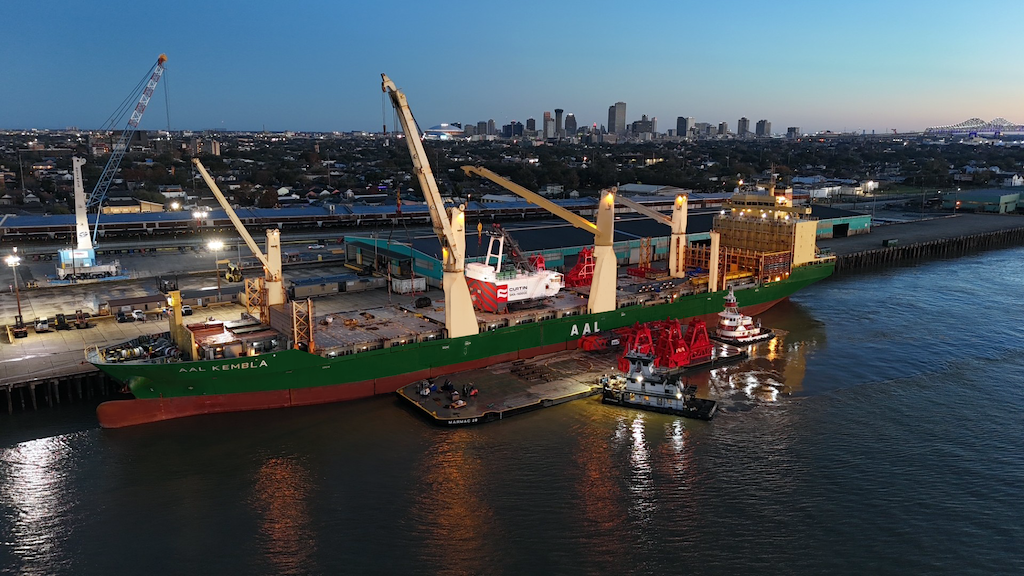
Upon arrival in New Orleans, the original discharge plan involved using a floating crane to offload the cargo onto a client’s crane barge. However, a change in requirements led to AAL Kembla’s heavy lift cranes being deployed again to discharge the cargo directly onto a material barge.
“Cargo operations involving loading or discharge onto barges are always tricky, especially when dealing with components as large and heavy as these,” explained Pacifico. “We conducted multiple stability simulations to ensure each stage of the operation adhered to established safety limits, even with the challenging weight distribution. This careful planning of the discharge sequence and cargo positioning was essential to maintaining sufficient stability for each heavy lift operation.”
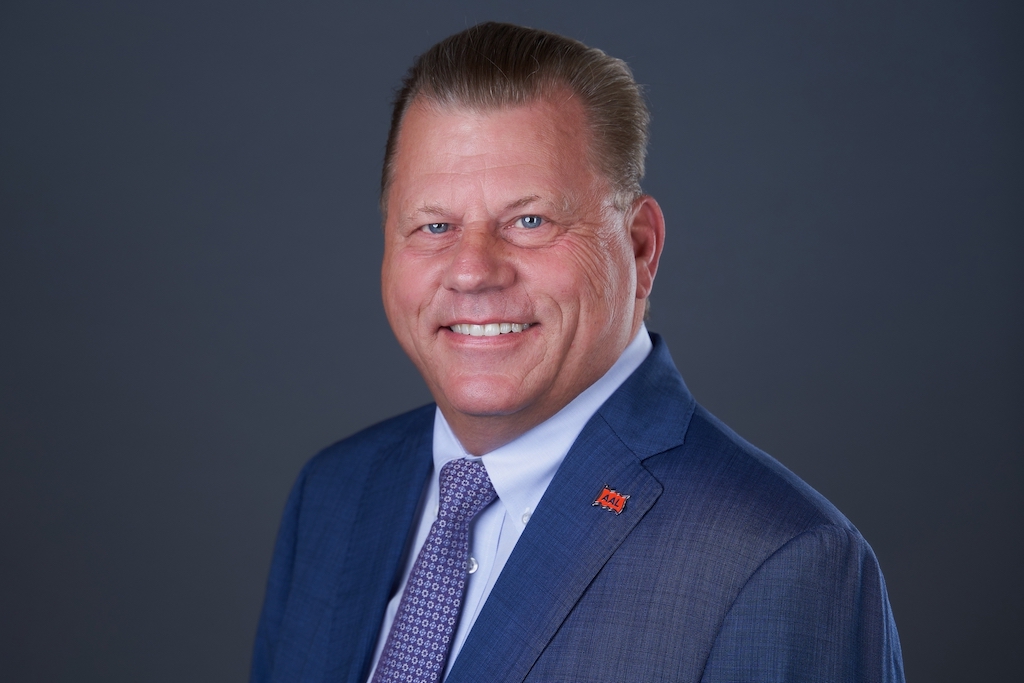
Henrik Hansen, General Manager of AAL Americas, concluded: “This operation demonstrates AAL’s ability to remain flexible and apply engineering expertise to tackle complex logistical challenges. Coordination between our commercial, engineering, and operational teams, along with effective communication with the client, played a key role in the success of this project. At several points during the shipment, we had to adjust our plans and develop new solutions to ensure the operation ran smoothly. It’s this level of commitment and adaptability—combined with the regularity and capacity of our Asia – Americas Trade Route—that makes AAL a trusted partner for customers in need of specialized heavy lift services.”