Mammoet has unveiled an innovative solution to address the growing challenges of transporting and storing massive XXL monopiles for offshore wind turbines. These cylindrical steel foundations, which anchor turbines to the seabed, can exceed 3,000 tonnes in weight and stretch over 120 meters in length.
As wind turbines grow taller, the dimensions of their foundations have also increased, surpassing the capabilities of existing handling equipment. This has led to difficulties in both transporting these enormous structures to the installation site and storing them effectively.
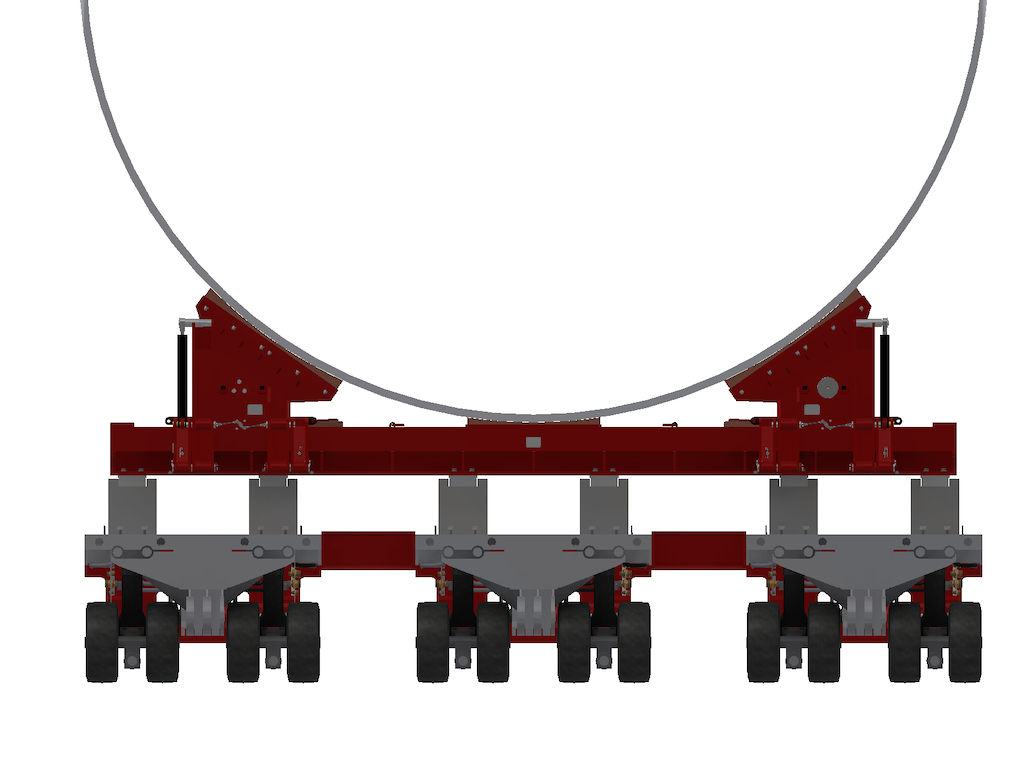
One issue arises from the deformation that occurs when lifting XXL monopiles due to their substantial self-weight. To load or unload them, they need to be raised higher than their support structures.
Mammoet’s newly developed jacking and cradle system addresses this challenge by providing an additional 60cm of stroke compared to standard Self-Propelled Modular Transporter (SPMT) systems. This extension allows customers to continue using their existing support structures as monopiles continue to grow in size.
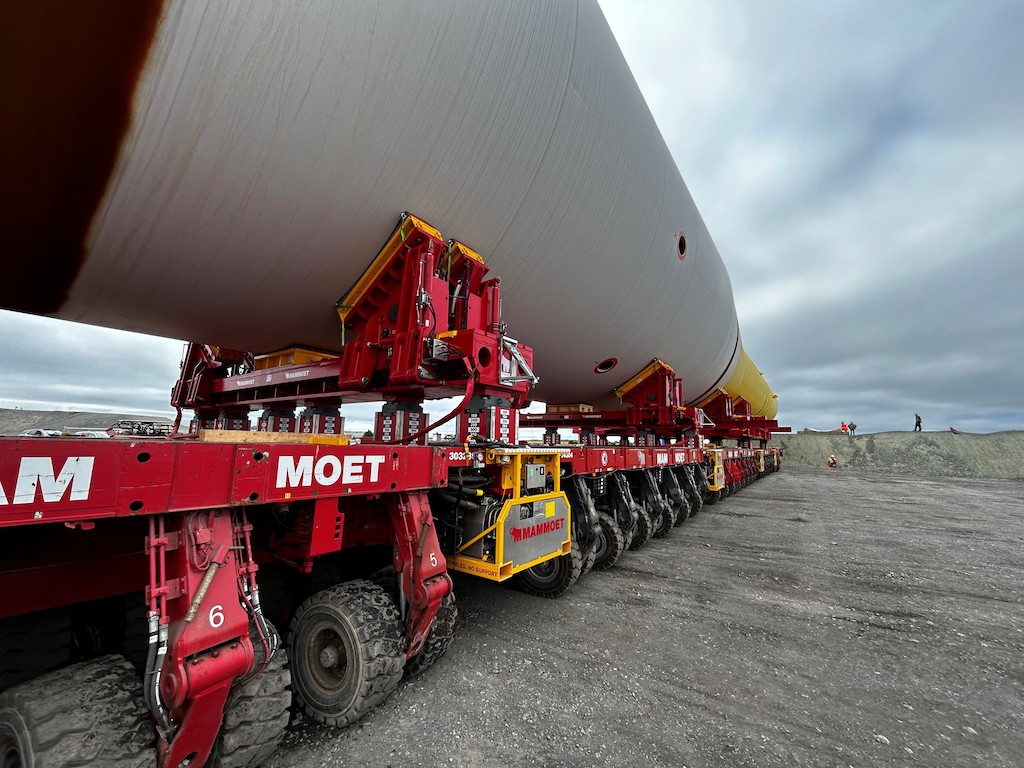
Furthermore, this technology offers cost-saving benefits for various stakeholders in the supply chain. As offshore wind projects expand globally, monopiles must travel longer distances, requiring Heavy Transport Vessels to have larger sea fastenings for support during transit. This presents challenges when using SPMTs to load and unload monopiles due to reduced clearance.
Mammoet’s jacking and cradle system solves this problem by enabling monopiles to be lifted higher, accommodating existing support structures. The system consists of two key components: jacking spacers, which fit between SPMT modules to provide increased stroke, and hydraulic, foldable saddles that cradle the monopile to support it at higher points and prevent excessive ovalization.
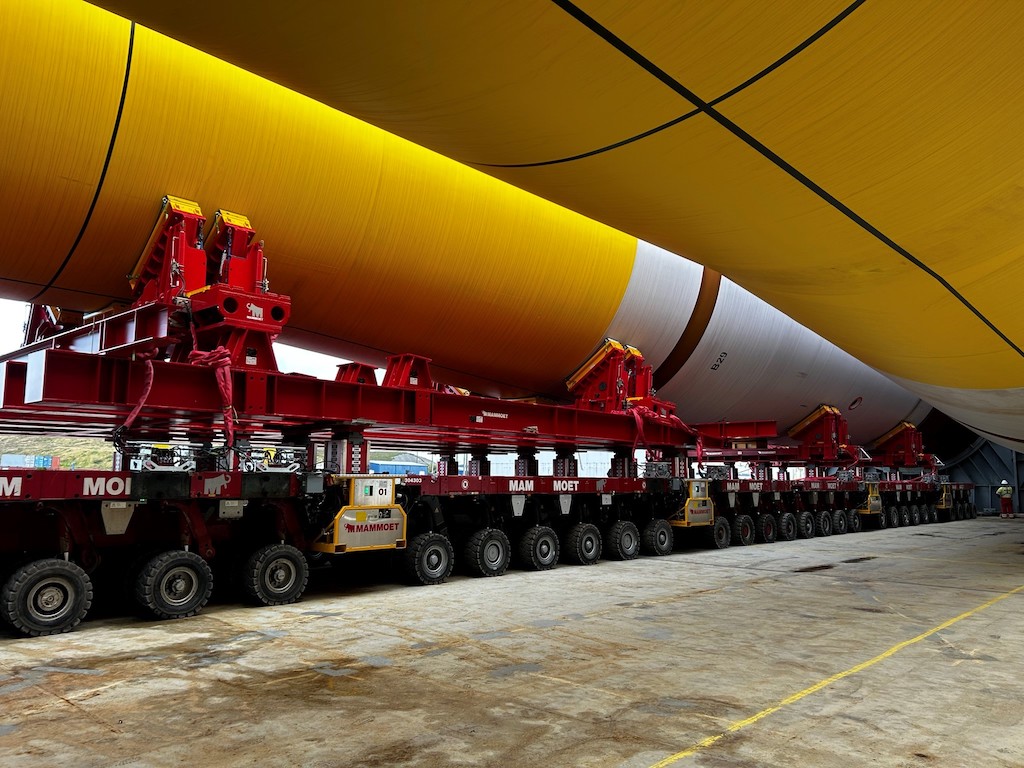
Each jacking spacer has a capacity of 430 tonnes, distributed across two towers, with multiple units used per transport configuration. These spacers fit seamlessly between SPMT modules, maintaining the same minimum ride height. This design keeps grillages and sand bunds as low as possible, resulting in cost savings.
The monopile saddle, with a capacity of 1,000 tonnes, can handle monopiles up to 12 meters in diameter. By adopting this system, Mammoet’s customers can maintain their existing methods of supporting and transporting monopiles, even as they increase in size from 8 meters to 10 meters and beyond. This approach reduces overall project costs across the fabrication, shipping, and storage supply chains.