Regina Leite, Global Head of Product Marketing, IEC Low Voltage Motors at ABB, explains that vehicle electrification isn’t just good for the planet – it’s better for an operator’s bottom line and employee wellbeing.

Electrification is essential to reaching Net Zero. Today, transport accounts for more than a quarter of the world’s total energy use and around 30% of total CO2 emissions. Industrial vehicles account for nearly half of these emissions.
Material handling vehicles – those that move shipping containers and industrial pallets around ports, airports and logistic centres – stand to benefit hugely from electrification. In addition to the immediate benefit of reducing emissions, there are significant advantages in terms of noise reduction, air quality, health outcomes, better control, and more. Electric powertrains are already available and proven for forklifts of all sizes, reach stackers, towing tractors, automated guided vehicles, terminal tractors, and other material handling vehicles.
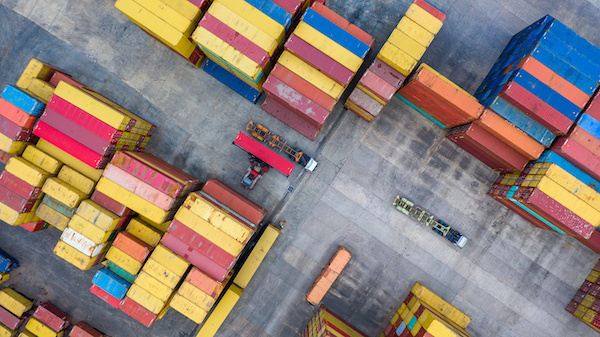
Why electrify industrial vehicles?
Modern electric technology including motors, drives and batteries are ideal for material handling vehicles for several reasons. Mechanically, electrical powertrains have fewer moving parts, making them more reliable and generally longer lasting than internal combustion engine (ICE) vehicles.
A standard diesel motor can typically operate for a total of approximately 12,000-15,000 hours, while electric motors have an average lifespan of over 20,000 hours. Electric motors can also achieve 95% energy efficiency within the optimum load range, while diesel engines can only reach a maximum of around 45% efficiency.
Electric motors also provide higher torque control and lower inertia, making it easier for operators to control machinery. Better control saves time and improves productivity. For example, a forklift operator moving pallets with an electric drivetrain will be more likely to align them correctly the first time, increasing throughput.
Electric vehicles are also superior in terms of air quality. ICE material handling vehicles produce dangerous fumes, including sulfur and nitrogen oxides. Inhaling fumes is harmful to employees and can exacerbate respiratory conditions. Emissions are a particularly significant issue in enclosed environments, such as warehouses.
To limit these dangerous emissions, ICEs use different kinds of exhaust after-treatment systems. Some of these systems are very complex as they house many different components. This increases the risk of unwanted downtime and the cost of the machine. By comparison, electric drivetrains do not produce emissions and no exhaust system is needed. This is better for employee wellbeing and reduces the amount of maintenance required.
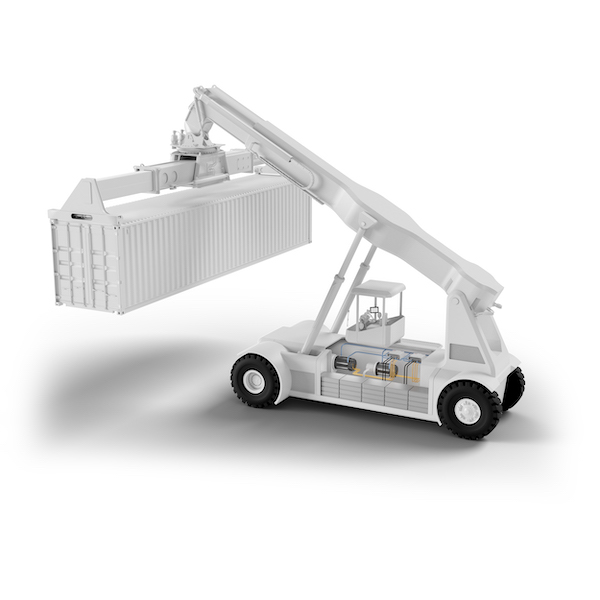
Electric vehicles are also far quieter than ICE vehicles, which reduces noise pollution and the need for hearing protection. It also makes the operating environment safer, especially on sites where materials are regularly moved between indoor and outdoor environments. Electric drivetrains also produce a smoother ride and less vibration, making it more comfortable to sit in a vehicle for extended periods.
Operators can sometimes be concerned by the upfront cost of electric vehicles. While the initial cost is slightly higher than ICE alternatives, the price is just a small part of the total cost of ownership (TCO). Electric vehicles have operating costs that are as much as 60% lower than ICE vehicles, on average. This is the result of greater “tank-to-wheel” efficiency, the cost of electricity compared with fuel and lower maintenance requirements. As a result, the TCO for electric materials handling vehicles is approximately 20% lower than equivalent ICE vehicles.
What makes electric materials handling vehicles different?
The key parts of an electric powertrain are the electric motor and the traction converter. As industrial vehicles, the electric motor must be more robust than those intended for consumer applications, particularly when operating 24 hours per day in some of the world’s major ports. A smaller forklift may depend on one electric motor for all its functions, including traction and movement of the forks. However, there are benefits to separating these operations and using two motors. Selecting dedicated motors for each function is more energy efficient and, because each motor can be smaller, is generally less expensive.

The traction converter is responsible for supplying the motor with electricity at the right voltage and frequency. This affects all other components in the powertrain, so it is essential that the traction converter is as efficient as possible. Fortunately, modern converter technology can cut energy use – and therefore operating costs – by up to 20%. Further improving efficiency, electric motors and traction converters can support regenerative braking.
Just like ICE vehicles, electric vehicles require infrastructure. Electric vehicles can receive power directly, such as through overhead catenaries, or recharge onboard batteries – or a combination of the two. Operators must consider the vehicle’s needs and specify the appropriate infrastructure. For example, in ports around the world, we are seeing more and more trolley-based electrification solutions. A trolley comes down from a mast to give a fast charge before the vehicle moves on. In this way, the vehicle is charged at certain key points but, unlike with catenaries, the vehicle is not forced to follow a set route.
For sites that opt for battery charging, this can be timed to intersect with employee breaks. This ensures that the equipment’s needs never restrict working. However, the large peak loads produced by this may require additional electrical infrastructure, such as battery storage. Where specific performance characteristics are required, it is also possible to adopt a hybrid approach that combines diesel engines and electric motors, using each where they are most efficient.
How do we electrify the industry?
The key to rolling out electrification is to build strong partnerships between OEMs, system integrators and operators. This ensures expertise on all sides, enabling the rapid rollout of new vehicles and the possibility of retrofitting diesel vehicles.
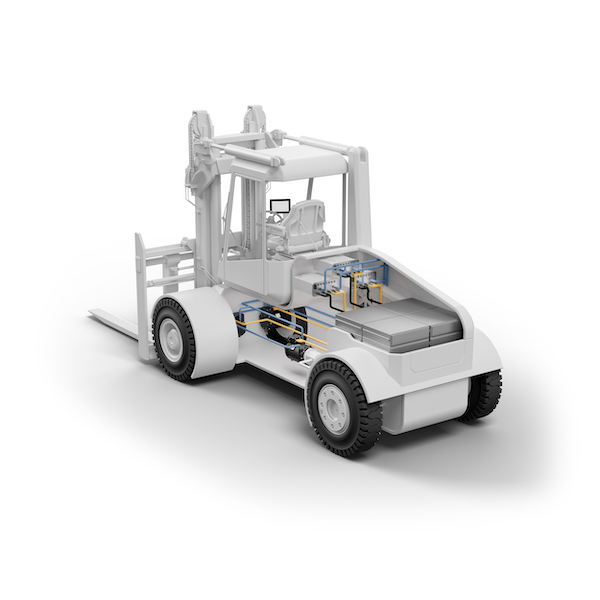
For example, ABB has partnered with Nasta AS in Norway to refit existing Hitachi vehicles with electric powertrains. Just one diesel-driven 24-tonne vehicle typically consumes around 18,000 liters of fuel each year, resulting in 48 tonnes of CO2 emissions – plus significant sulfur oxide (SOx) emissions.
ABB and Nasta AS have successfully upgraded several vehicles with electric powertrains, improving on-site air quality and noise levels. Operators also report that the machines are noticeably more responsive. In short, electrification is a cost-effective way to reduce the industry’s carbon emissions, as well as producing a safer and more pleasant workplace.
Download ABB’s whitepaper on sustainable transport to learn more about the transformative role electrical powertrains can play in industrial transportation.