Modulift has manufactured and delivered two custom lifting frames for the High Speed 2 (HS2) project, all within 6 weeks from the initial contact. The infrastructure project, which is currently the largest in Europe, will provide a welcome boost to the economy with an estimated budget of £106bn. As well as providing faster rail links, with trains reaching speeds of up to 250mph, the Dept of Transport forecast that there will be 2,000 apprenticeships and 25,000 people employed across the project. Modulift’s team of engineers were asked to provide a custom lifting solution that would lift high speed railcar panels with a lifting capacity of 25t, in two separate locations. The first lifting frame is being used at Southampton Docks, where headroom isn’t an issue. Whilst the second custom lifting frame is at DB Schenkers Immingham warehouse facility, where a low height solution is required.
Two lifting frames
Both Modulift custom lifting frames were of the same design, with one having additional components to facilitate the low height requirement. Each custom lifting frame was designed with a span of 19m by 3m and a lifting capacity of 25t. Four top lifting lugs were included to enable both lifting frames to be used at a standard lift height. The second custom lifting frame was designed to have four additional top lifting lugs. The addition of the lugs enabled the slings to be attached at a closer point from the centre of the lifting frame for the low height specification. Therefore, the second custom lifting frame offers both low height and standard height lifting solutions, as it can be used inside and outside the warehouse facility when required.
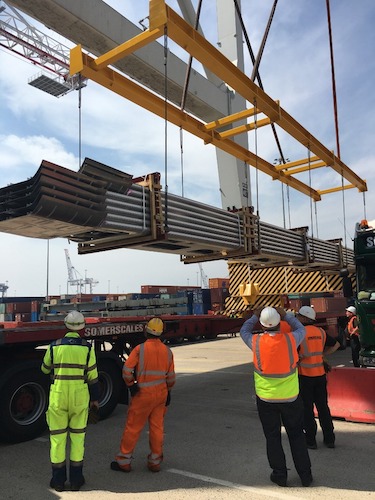
Modular design
Modular in design, the frames were manufactured in 3 sections, along with cross beams that added strength and stability which are bolted on site. This made transportation of the custom lifting frames easier, which is a design feature that Modulift are well-known for across their whole range of spreader beams, spreader frames and lifting solutions. Modulift’s senior project engineer, Matt Roberts, was on site to oversee the first of the two custom lifting frames being put together for the first lift in Southampton, where there was a team of 8 stevedores – 4 on the ship, and 4 on the quay, to manage the lift. Planning for the lifts began in March 2020, which sees the lift of 18 high speed railcar panels per vessel from a total of 7 vessels which is due to complete in March 2021.
Harshal Kulkarni, Engineer Manager at Modulift said: “One of the lifting frames had a unique design due to its low height application. The slings were specially designed for a low headroom requirement. The slings are normally used at standard base angles of 0-45 degrees. In this case the slings were designed for base angles of 30-60 degrees. Hence, requiring a special design and set of calculations. The lifting lugs were also specially designed for added compression due to acute base sling angles”.